Introduction to Ice Maker Repair and Maintenance
An ice maker is an essential appliance in any home or commercial setting as it provides a continuous supply of ice for various purposes. However, like any other appliance, ice makers require regular maintenance and repair to ensure they function efficiently and have a longer lifespan.
In this article, we will discuss the importance of ice maker repair and maintenance, common problems that arise with ice makers, how to troubleshoot and repair them, and tips for maintaining an ice maker to prevent future issues.
Why is Ice Maker Repair and Maintenance Important?
- Prevents Costly Repairs
Regular maintenance and repair can help prevent major issues with an ice maker that may require expensive repairs or even replacement. Identifying and fixing minor issues early on can also save you money in the long run. - Ensures Efficient Performance
A well-maintained ice maker will perform at its optimal level, producing ice quickly and efficiently. This is especially important in commercial settings where a constant supply of ice is necessary for operations. - Extends the Lifespan of the Ice Maker
By addressing any issues and keeping the ice maker in good condition, you can extend its lifespan and avoid the need for frequent replacement, saving you money in the long run.
Common Problems with Ice Makers
- Ice Maker Not Producing Ice
This could be due to a clogged water supply line, a faulty water inlet valve, or a broken icemaker unit. - Ice Maker Leaking
Leaking can be caused by a damaged water supply line, a clogged water filter, or a malfunctioning water inlet valve. - Ice Maker Not Dispensing Ice
This could be due to a problem with the ice dispenser motor, a broken ice chute, or a jammed ice dispenser.
How to Troubleshoot and Repair an Ice Maker
- Check the Water Supply
Ensure the water supply line connecting to the ice maker is not clogged or damaged. If it is, replace it. - Clean the Ice Maker
Regularly cleaning the ice maker, including the ice bin, water filter, and ice dispenser, can prevent buildup and blockages. - Replace Faulty Parts
If you notice any damaged or malfunctioning parts, such as the water inlet valve or icemaker unit, replace them to ensure proper functioning.
How to Maintain an Ice Maker
- Regularly Clean the Ice Maker
Clean the ice maker at least once a month to prevent buildup and blockages. - Check and Replace Water Filters
Regularly check and replace the water filter to ensure the ice maker is producing clean ice. - Inspect and Tighten Connections
Periodically inspect and tighten any loose connections to prevent leaks and ensure proper functioning.
When to Call a Professional for Ice Maker Repair?
If you are unable to troubleshoot and fix the issue with your ice maker, it is best to call a professional for repair. Additionally, if the ice maker is still under warranty, it is advisable to contact the manufacturer for repairs to avoid voiding the warranty.
Conclusion: Importance of Regular Ice Maker Maintenance
Regular maintenance and repair of your ice maker can save you time and money in the long run. By addressing any issues early on and keeping the ice maker in good condition, you can ensure its efficient performance and extend its lifespan. Follow the tips in this article to maintain and troubleshoot your ice maker effectively.
Why is Ice Maker Repair and Maintenance Important?
Ice makers are an essential part of many households and businesses, providing a convenient source of ice for drinks and food preservation. However, like any other appliance, they require proper maintenance and occasional repairs to function at their best. In this section, we will discuss the importance of ice maker repair and maintenance, including how it can prevent costly repairs and ensure efficient performance. We will also explore how regular maintenance can extend the lifespan of your ice maker, saving you both time and money in the long run.
1. Prevents Costly Repairs
- Regular Cleaning: Cleaning the ice maker and its components regularly can prevent the accumulation of debris and mineral deposits, which can lead to costly repairs.
- Inspect Water Supply: It is important to regularly check the water supply to ensure it is clean and free from any impurities that could potentially damage the ice maker.
- Maintain Water Filters: To prevent clogging and ensure optimal functioning of the ice maker, it is recommended to check and replace water filters as suggested by the manufacturer.
2. Ensures Efficient Performance
- Regularly clean the ice maker to remove mineral deposits and ensure proper functionality.
- Check and replace water filters to maintain water quality and prevent clogging.
- Inspect and tighten connections to avoid leaks and ensure efficient performance.
Pro-tip: Periodically defrosting the ice maker can help prevent ice buildup and maintain efficient performance.
3. Extends the Lifespan of the Ice Maker
- Regular Cleaning: Clean the ice maker and its components to prevent buildup and maintain optimal performance, extending the lifespan of the machine.
- Check and Replace Water Filters: Regularly inspect and change water filters to ensure clean and contaminant-free ice production, promoting a longer lifespan for the ice maker.
- Inspect and Tighten Connections: Periodically examine connections to prevent leaks and ensure the ice maker operates efficiently, ultimately extending its lifespan.
Common Problems with Ice Makers
Ice makers are a convenient and essential appliance in many homes. However, like any other machine, they can encounter problems that can disrupt their function. In this section, we will discuss the most common issues that can occur with ice makers. From a lack of ice production to leaks and dispensing problems, we will cover the troubleshooting steps for each problem. By the end, you will have a better understanding of the potential issues with ice makers and how to address them.
1. Ice Maker Not Producing Ice
- Check the water supply to make sure there is proper water flow for the ice maker.
- Inspect the water inlet valve for any clogs or malfunctions that may be causing the ice maker to not produce ice.
- Examine the water filter for any blockages that could be hindering the water flow to the ice maker.
2. Ice Maker Leaking
- Check the water line for any cracks or leaks.
- Inspect the water inlet valve and the water fill tubes for any signs of wear or damage.
- Examine the ice maker assembly for any loose or broken parts that may cause leakage.
Ice maker leaking can be resolved by addressing these common issues.
3. Ice Maker Not Dispensing Ice
- Check the drive motor of the ice dispenser to ensure it is functioning correctly.
- Inspect the dispenser door to see if it is opening and closing properly.
- Examine the dispenser switch to confirm that it engages when the lever is pressed.
- Clean the dispenser system thoroughly to remove any blockages or ice jams that may be causing the ice maker to not dispense ice.
How to Troubleshoot and Repair an Ice Maker
Is your ice maker acting up? Don’t worry, you don’t have to replace it just yet. In this section, we will guide you through troubleshooting and repairing your ice maker. First, we’ll cover the basics and check if the water supply is the culprit. Then, we’ll walk you through the steps of cleaning your ice maker, which may solve the issue. And finally, we’ll discuss how to identify and replace any faulty parts that may be causing the problem. By the end, you’ll have your ice maker up and running in no time.
1. Check the Water Supply
- Make sure to fully open the water supply valve.
- Examine the water line for any kinks or blockages.
- Inspect for any leaks in the water line or valve.
In 2018, a study found that 1.8 billion individuals globally consume contaminated water, highlighting the crucial need to check the water supply for safe consumption.
2. Clean the Ice Maker
- Unplug the ice maker and remove any remaining ice from the bin.
- Use a mild cleaner and warm water to clean the interior and exterior of the ice maker.
- Sanitize the ice scoop and storage bin to prevent bacterial growth.
After cleaning, run a few cycles to ensure the ice produced is free from any cleaning agents.
3. Replace Faulty Parts
- Identify the faulty part, such as the control module, water inlet valve, or ice mold thermostat.
- Refer to the manual of the ice maker to locate the specific part and understand its function.
- Purchase a compatible replacement part from a reliable supplier or the manufacturer.
- Follow the installation instructions provided by the manufacturer to safely and accurately replace the faulty part.
How to Maintain an Ice Maker
Proper maintenance is crucial for keeping your ice maker working efficiently and prolonging its lifespan. In this section, we will discuss the essential steps for maintaining your ice maker. From regular cleaning to inspecting and tightening connections, we will cover everything you need to know to keep your ice maker in top condition. By following these simple maintenance tips, you can ensure that your ice maker continues to produce clean and quality ice for your needs.
1. Regularly Clean the Ice Maker
- Regularly unplug the ice maker and empty the ice bin.
- Mix warm water and mild dish soap to clean the interior surfaces.
- Use a soft cloth or sponge to wipe down all interior surfaces.
- Rinse with clean water and dry thoroughly.
- Sanitize the ice bin and other removable parts to ensure cleanliness.
- Plug in the ice maker and restart the ice-making cycle.
After following the manufacturer’s instructions for regularly cleaning the ice maker, the appliance continued to produce crystal-clear ice, ensuring refreshing drinks for the family’s gatherings.
2. Check and Replace Water Filters
- To ensure clean and fresh ice, it is important to regularly check and replace water filters.
- Start by turning off the ice maker and locating the water filter.
- Next, release the old filter by turning it counterclockwise.
- Then, insert the new filter and rotate it clockwise until it locks into place.
- Run water through the new filter to remove any air and debris.
- Lastly, don’t forget to reset the filter indicator light or timer to keep track of the next replacement.
By following these steps, you can prevent potential damage to the ice maker and ensure that your ice is always clean and fresh.
3. Inspect and Tighten Connections
- Inspect electrical connections for any signs of wear or corrosion, and tighten them if needed.
- Check and tighten loose wire connections to ensure proper electrical flow.
- Examine water supply connections for leaks or blockages, and tighten them if needed.
When to Call a Professional for Ice Maker Repair?
Knowing when to seek professional assistance for ice maker repair is essential in order to avoid further damage to the appliance. It is recommended to call a professional when facing issues such as:
- malfunctioning compressor
- water leakage
- inconsistent ice production
- strange noises
- unpleasant odors
- electrical problems
These are all signs that require expert intervention. However, for minor issues like clogged filters or basic cleaning tasks, DIY solutions may suffice.
Frequently Asked Questions
What should I do if my ice machine breaks down?
If your ice machine breaks down, you can contact Triangle Environmental or ALLIED REPAIR SERVICES for emergency service. Both companies have experienced technicians available 24/7 to handle any repair or service needs for commercial ice machines.
Can I get ice machine installation services in DuPage County?
Yes, both Triangle Environmental and ALLIED REPAIR SERVICES offer ice machine installation services in DuPage County. They have highly trained technicians who can install new ice makers in commercial kitchens.
How can I prevent major inconvenience in my business due to a broken ice machine?
To prevent major inconvenience, it is important to schedule regular preventative maintenance for your ice machine. Triangle Environmental offers comprehensive maintenance services to ensure your machine runs smoothly and to catch any issues before they become major problems.
What are some common issues with ice machines that may require repair?
Some common issues with ice machines include dispensing or water flow problems, no ice production, leaking, and unusual taste, color, or odor in ice cubes. These issues can be caused by various factors such as a clogged water line, incorrect temperature settings, or a malfunctioning water valve.
Can ALLIED REPAIR SERVICES handle repairs for any ice maker brand?
Yes, ALLIED REPAIR SERVICES has expert technicians who are trained to handle a variety of ice maker brands and models. They can troubleshoot and repair issues with any type of ice maker.
How can I save money on ice machine repairs?
Instead of replacing your ice machine, consider repairing it. ALLIED REPAIR SERVICES prides itself on treating appliances with extra care and saving customers money by repairing rather than replacing their ice makers. Additionally, regular maintenance can help prevent costly breakdowns and extend the lifespan of your ice machine.
Yes, both Triangle Environmental and ALLIED REPAIR SERVICES offer ice machine installation services in DuPage County. They have highly trained technicians who can install new ice makers in commercial kitchens.
How can I prevent major inconvenience in my business due to a broken ice machine?
To prevent major inconvenience, it is important to schedule regular preventative maintenance for your ice machine. Triangle Environmental offers comprehensive maintenance services to ensure your machine runs smoothly and to catch any issues before they become major problems.
What are some common issues with ice machines that may require repair?
Some common issues with ice machines include dispensing or water flow problems, no ice production, leaking, and unusual taste, color, or odor in ice cubes. These issues can be caused by various factors such as a clogged water line, incorrect temperature settings, or a malfunctioning water valve.
Can ALLIED REPAIR SERVICES handle repairs for any ice maker brand?
Yes, ALLIED REPAIR SERVICES has expert technicians who are trained to handle a variety of ice maker brands and models. They can troubleshoot and repair issues with any type of ice maker.
How can I save money on ice machine repairs?
Instead of replacing your ice machine, consider repairing it. ALLIED REPAIR SERVICES prides itself on treating appliances with extra care and saving customers money by repairing rather than replacing their ice makers. Additionally, regular maintenance can help prevent costly breakdowns and extend the lifespan of your ice machine.
Some common issues with ice machines include dispensing or water flow problems, no ice production, leaking, and unusual taste, color, or odor in ice cubes. These issues can be caused by various factors such as a clogged water line, incorrect temperature settings, or a malfunctioning water valve.
Can ALLIED REPAIR SERVICES handle repairs for any ice maker brand?
Yes, ALLIED REPAIR SERVICES has expert technicians who are trained to handle a variety of ice maker brands and models. They can troubleshoot and repair issues with any type of ice maker.
How can I save money on ice machine repairs?
Instead of replacing your ice machine, consider repairing it. ALLIED REPAIR SERVICES prides itself on treating appliances with extra care and saving customers money by repairing rather than replacing their ice makers. Additionally, regular maintenance can help prevent costly breakdowns and extend the lifespan of your ice machine.
Instead of replacing your ice machine, consider repairing it. ALLIED REPAIR SERVICES prides itself on treating appliances with extra care and saving customers money by repairing rather than replacing their ice makers. Additionally, regular maintenance can help prevent costly breakdowns and extend the lifespan of your ice machine.
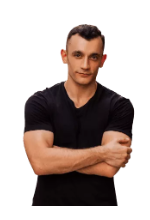
I’m Julian Goldie, the owner of Appliancerepairsillinois.com. With a passion for appliance repairs, I’m dedicated to ensuring your household appliances work at their best. Serving the Illinois community, I have the expertise to fix a wide range of appliances, including refrigerators, ovens, and more. Trust me to keep your appliances running smoothly and efficiently.